围绕智能机电装备系统设计与健康运维展开研究,主要研究方向包括智能机电装备技术开发、智能检测与优化技术的研究。
团队成员:文广、吴昱东
1. APS自动上料设备技术开发
本项目聚焦芯片前端制造工艺段,以六轴机械臂为核心载体,开展多功能一体式末端夹具的创新设计与应用研究。研究内容涵盖末端夹具的结构优化、功能集成以及与机械臂的协同控制开发,通过精密的机械结构设计与智能控制算法,使末端夹具具备多种物料抓取、精准定位及自适应调整能力,可适配不同规格的物料盘。
项目应用了AGV自动导引技术、机械臂运动规划算法、视觉识别定位系统等关键技术。AGV能够根据预设路径自动搬运物料栈至指定工位,机械臂结合视觉识别系统,可精准识别物料盘位置与姿态,并依据芯片制造工艺要求,通过优化后的运动规划算法,按照既定顺序依次抓取物料盘,准确放置到各工艺工位。
该项目有效解决了芯片前端制造中人工上料效率低、错误率高的行业痛点。经实际验证,相比传统人工操作,生产效率显著提升,人工错误率降低幅度超过90%,大幅提高了生产的稳定性与产品良率。项目成果主要应用于芯片制造企业的前端工艺生产环节,助力企业实现生产流程的智能化升级,降低人力成本,提升行业竞争力。
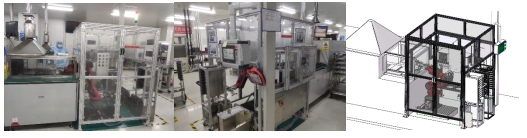
技术指标
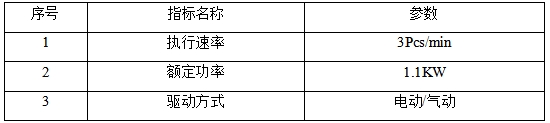
2. SMC自动上料设备技术开发
本项目专注于SMC封装芯片可靠性检测领域,致力于研发一套高度自动化的热冲击实验设备。该设备以实现全流程无人化操作为目标,集成了智能物料处理与精确环境模拟两大核心功能模块。在物料处理方面,通过高精度称重传感器与智能分拣算法,实现芯片的自动计重分料;结合定制化的上料机构与视觉定位系统,可精准控制单次上料数量,并确保芯片物料在实验承载平台上完全平铺、无重叠摆放,有效规避传统人工操作中可能出现的物料堆积或错位问题。
项目应用了多轴联动控制技术、闭环温度控制系统及自动化流程管理系统等关键技术。其中,闭环温度控制系统可根据实验需求,将实验舱内温度快速、精准地加热至设定的冲击温度,并保持稳定的保温状态;自动化流程管理系统则对加热、保温、冷却环节进行智能化调控,严格按照预设程序完成三次温度循环,确保实验数据的一致性与可靠性。
该设备的成功研制,有效解决了传统SMC封装芯片热冲击实验中存在的人工干预多、实验效率低、数据离散度大等行业难题。通过全自动化操作,不仅显著提升了实验效率与数据准确性,还降低了人为操作导致的实验误差与设备损耗风险。
本设备主要应用于半导体封装测试企业、电子元器件研发机构等场景,为SMC封装芯片在极端温度环境下的性能评估与可靠性验证提供标准化、智能化的实验解决方案,助力企业加速产品研发进程,提升产品质量与市场竞争力。
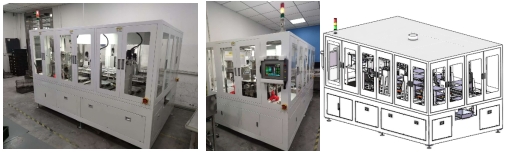
技术指标
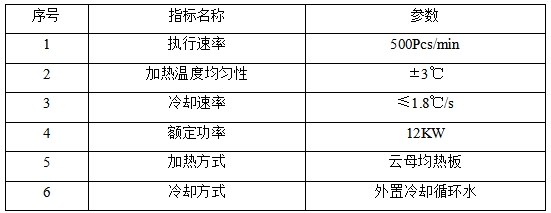
3.多轴运动平台技术开发
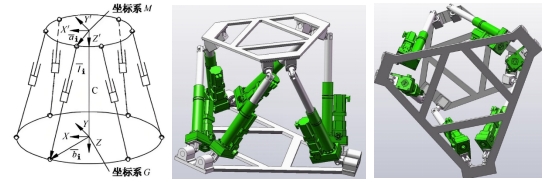
本项目聚焦高精度运动控制领域,围绕六轴运动平台开展系统性技术研发,旨在突破传统运动平台的精度与自由度限制,构建具备卓越性能的六自由度位移运动系统。项目以伺服直线电缸为核心执行单元,单轴配置高精度伺服直线电缸,通过六台伺服直线电缸的协同集成,实现顶部平台在空间六个自由度(沿X、Y、Z轴的直线移动与绕X、Y、Z轴的旋转运动)的精准操控。
在关键技术层面,项目深度融合伺服驱动控制技术、多轴联动协同算法、运动学建模与逆解技术。其中,伺服直线电缸凭借高响应速度、高定位精度及大负载能力的特性,确保单轴运动的稳定性与准确性;多轴联动协同算法通过对六台伺服直线电缸的实时协调控制,实现平台复杂轨迹运动;基于运动学理论构建的数学模型及优化后的逆解算法,可快速将目标运动参数转化为各轴驱动指令,显著提升平台运动控制的实时性与精准度。
该项目有效解决了传统运动平台存在的运动精度不足、响应速度慢、多自由度协同控制困难等问题。通过六轴高精度伺服直线电缸的应用与创新控制技术,大幅提升平台运动的定位精度、动态响应能力与负载适应性,可满足微米级甚至亚微米级的高精度运动需求,有效避免因运动误差导致的生产质量问题,显著提高加工或检测效率。项目成果广泛适用于半导体制造、精密加工、自动化检测、医疗设备、航空航天等对运动精度与自由度要求严苛的领域。
技术指标
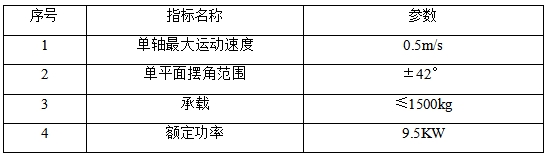
4.基于大数据聚类分析的减振器异响在线甄别系统
悬架减振器异响问题长期以来是影响整车舒适性与品质感知的核心难点之一。传统异响识别方法主要依赖人工听音和主观判断,不仅诊断效率低下,而且存在较高的误判率(行业平均误判率约为25%)以及较长的排查周期(单件检测时长约为4–6小时),严重制约了质量控制的时效性与稳定性。针对上述痛点,本项目团队依托多年在减振器异响机理分析与治理方面的工程积累,构建了一套基于大数据驱动的聚类分析与分类识别融合模型,提出了“多指标柔性判定机制”,即将传统的单一刚性矩形阈值判断模式,转化为多维度特征空间下的柔性圆形包络区域。该方法有效降低了因单特征波动而引发的误判风险,显著提升了异响识别的鲁棒性与准确性。依托上述模型算法,所开发的在线甄别系统在实验验证与产线部署中均表现出优异的性能表现。核心识别算法的预测准确率稳定达到99.5%以上,远超行业对标值。系统部署后,企业减振器异音类客户投诉率由原先的接近1%降至0.1%以下,实现了从“事后返修”向“过程预防”转变的质量管理模式升级。
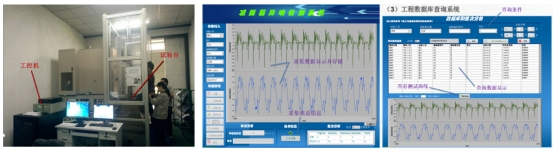
本系统已成功应用于西南地区某知名减振器制造企业的总装产线中,助力其建立起具有前瞻性的智能化质量识别能力,进一步提升了产品一致性与品牌竞争力。未来,该系统亦具备在其他汽车关键零部件异响检测场景中推广应用的潜力,对行业智能质控能力提升具有良好的示范价值。
5.新能源汽车分布式驱动“机-电-磁-网”多模动态性能试验平台
项目技术团队攻克了电动轮动载荷实时精确估计技术,建立了电动轮动态载荷估计统一模型,形成了融合动态质心的动载荷估计方法;项目技术团队攻克了系统时滞动态模拟与跟踪控制技术,掌握了实验系统时滞特性分析技术,形成了机-电-磁-网系统集成设计技术。
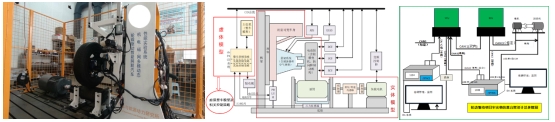
6.基于自主学习的汽车声学包性能智能预测与优化系统
传统试验以及仿真方法进行声学包吸隔声性能预测在求解和计算效率上处于劣势,因此本团队另辟蹊径,采用智能化的数据驱动方法对声学包隔吸声性能进行预测,对已有数据的使用价值进行深度挖掘,提高了声学包开发效率,从而协助工程师从繁琐的声学理论建模中解脱。建立了较为完备的声学包整车-系统-部件-平板多层级性能多层级分解架构,并搭建了声学包基础数据库系统,在此基础上,发了声学包性能智能分析云平台系统,可用于声学包多目标性能快速预测、灵敏度分析与优化设计。相关研究内同已实现产品开发。
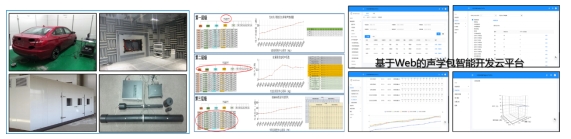